Grasping the depth of drop-in pitches
In Melbourne, Sidharth Monga tries to understand the science and logistics behind the idea of drop-in pitches, and that they are not as complicated as he expected
Sidharth Monga in Melbourne
24-Dec-2014
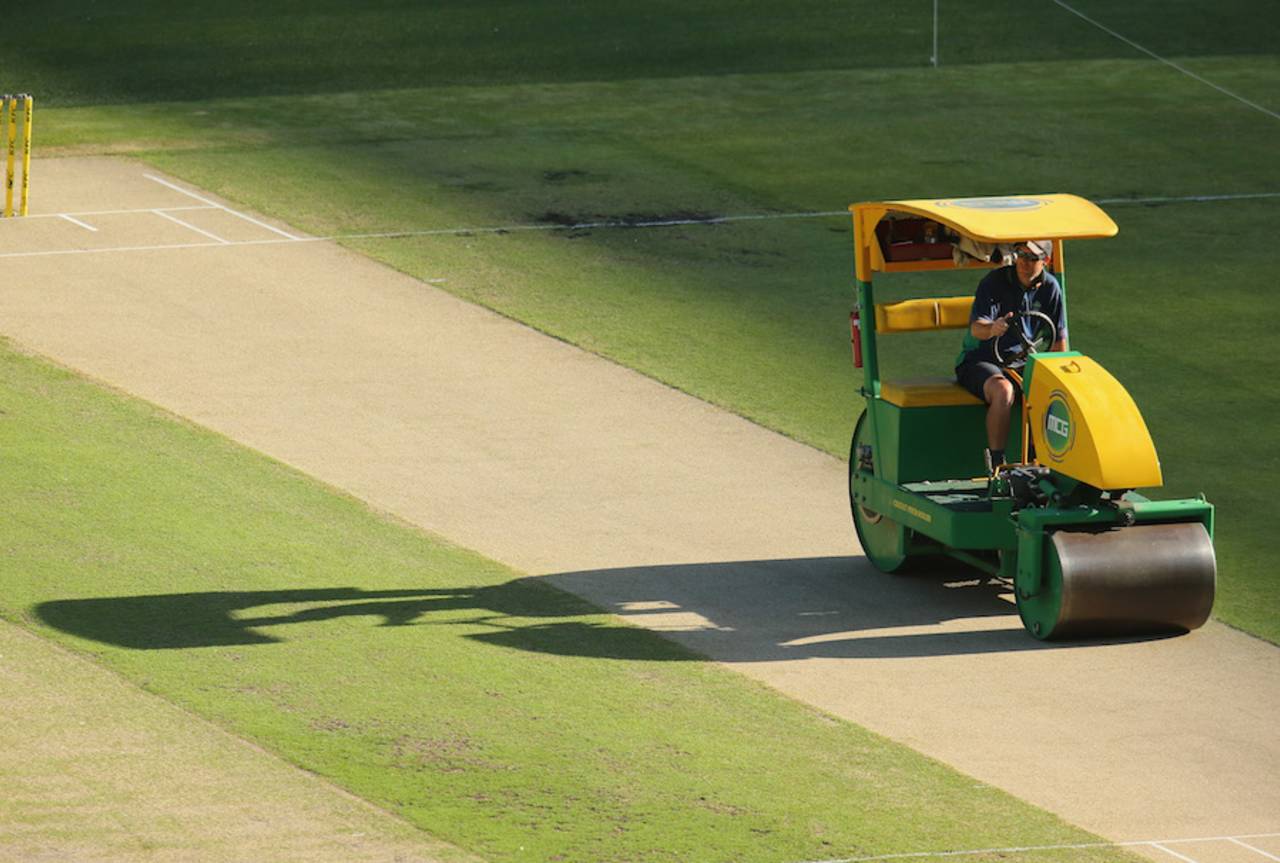
As many as 10 drop-in pitches are removed and put back at the MCG every season • Getty Images
When I first heard of drop-in pitches, I thought it involved closing air traffic in the Richmond area of Melbourne to bring it in carried by some 30 aircrafts. I also imagined secret simulated environs, a bit of a green house if you will, where mad scientists bring in the best possible soils to create this mythical creature called the drop-in pitch. I must say I'm a little disappointed it's not all of that. And David Sandurski, head groundsman at MCG, makes it sound even simpler. Important people all do that. VVS Laxman never understood what the fuss around his flicks from well outside off was.
Drop-in pitches are hard work - don't get me wrong - but a simpler, less dramatic, process than I thought. Especially in Australian grounds - where footy and cricket seasons don't clash - the installation and removing has to be done only once each year. I've seen in Christchurch a pitch being brought in a day before a T20 match and then removed minutes after the conclusion. Here in Australia, at MCG for example, they remove the pitches - 10 of them - in the off season and leave them in an open ground near the G. They keep working on them during the off season - on the foot holes, tending to grass etc. - but they leave it open to the elements. The actual work on the pitches begins when they are installed in the ground.
The pitches are in a steel frame - a cake tin, if you will. They are 24 metres long, three metres wide and 200 millimetres deep. They weight around 30 ton. MCG brought the concept 14 years ago, and is using the same pitches still. That means they are durable. The work on them, the soil in them, the grass on top of them is pretty much similar to actual pitches.
The most taxing work starts when they have to be transported into the ground. One of the 10 brought in after the footy final this year will be the stage of the World Cup final. The machine that brings them in has to be as long and as wide, and weighs more than 30 ton. MCG has to get in touch with transport authorities a month in advance, and close out traffic for four nights on Brunton Avenue. They can bring in the 10 pitches over three nights, but they need a fourth night should the machinery break down. It cannot be repaired on the go, you see. They don't sell spares for such machines in usual mechanic shops. The process is repeated after the cricket season is over. It helps that the same staff looks after the ground during footy season too.
In the process I also realised that my biggest curiosity about drop-in pitches was stupid: why can't they get them to behave exactly like they want them to? The soil and the grass used for the pitches are same as the real ones used to use at the MCG. When they first began, the G had to do with slow and spongy bounce, but it is slowly getting back to its original nature. Adelaide Oval, the youngest drop-in pitch consumer in Australia, behaved more or less like the Adelaide Oval of the old in the first Test of this series. The drop-in pitches will continue to behave differently and retain old traits because the soil and the atmosphere where they are made doesn't change.
That drop-in don't crumble as much is a criticism they have to live with, although Adelaide Oval went a long way to disprove that. Still I can't forgive them for being accessory to the conspiracy of implanting ugly stands on the top of the lovely Adelaide Oval.
Sidharth Monga is an assistant editor at ESPNcricinfo